SSAB’s New $5 Billion in Fossil-Free Steel Mill to Eliminate 7% of Sweden’s CO2 Emissions
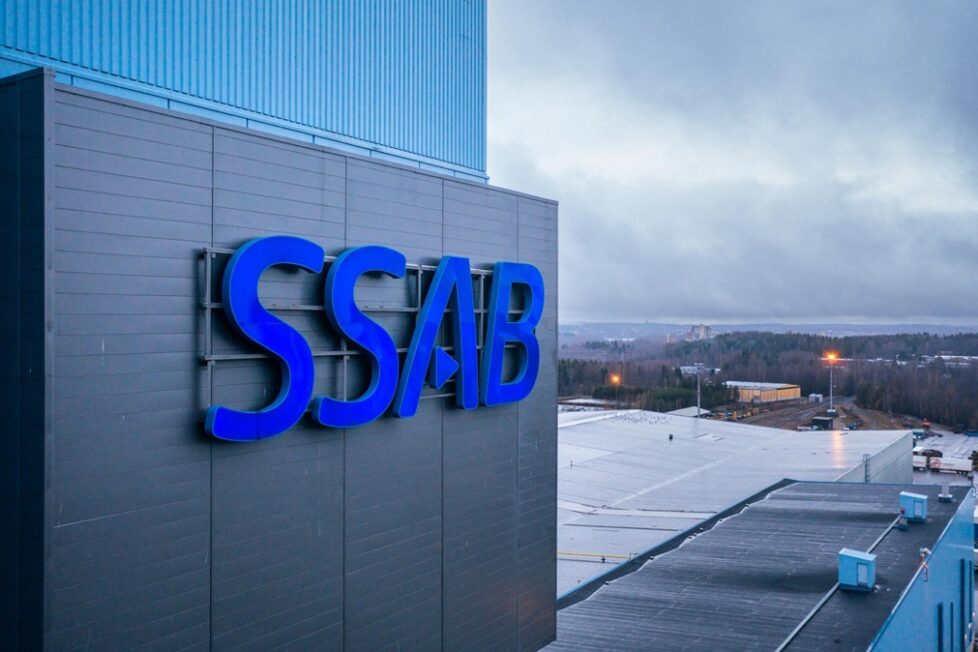
Sweden-based global steel company SSAB announced a decision to build a fossil-free mini-mill in Luleå, Sweden, capable of producing 2.5 million tonnes of carbon emission-free steel annually.
Total investment in the new mill is estimated at €4.5 billion (USD$4.9 billion), and the project is expected to reduce Sweden’s CO2 emissions by 7%.
Steelmaking is one of the biggest emitters of CO2 globally, with total greenhouse gas emissions (GHG) from the sector accounting for 7% – 9% of direct emissions from the global use of fossil fuels.
SSAB President and CEO Martin Lindqvist said:
“The transformation of Luleå is a major step on our journey to fossil-free steel production. We will remove 7% of Sweden’s carbon dioxide emissions, strengthen our competitive position and safeguard jobs with the most cost-effective and sustainable strip production in Europe.”
According to SSAB, the new mill will run on fossil-free electricity and use only fossil-free energy sources. The project will consist of two electric arc furnaces (EAFs) in place of blast furnaces. As opposed to burning coal, an electric arc furnace uses electric currents to create the heat needed to melt and mold metal. When completed, SSAB said that it will replace its current blast furnace-based production system.
The new mill will be supplied by carefully selected recycled scrap, as well as fossil free sponge iron from SSAB’s Hybrit demonstration plant. SSAB developed Hybrit in collaboration with Vattenfall and LKAB, replaces the coking coal traditionally used for iron ore-based steelmaking with fossil-free electricity and hydrogen producing water as a byproduct instead of carbon dioxide.
In addition to the environmentalEnvironmental criteria consider how a company performs as a steward of nature. More impact, SSAB outlined a series of other benefits anticipated from the investment in its new fossil-free mill, including a 0.5 million tonne annual increase in steel production, a mix improvement an increase share of special and premium steel grades, a broader product offering for the automotive and truck sectors, and financial improvements through lower fixed costs and eliminated carbon emissions costs.
Startup of the new mill is planned at the end of 2028 with full capacity one year later.