AWS Signs Deal for Fossil Free Steel for Data Center with SSAB
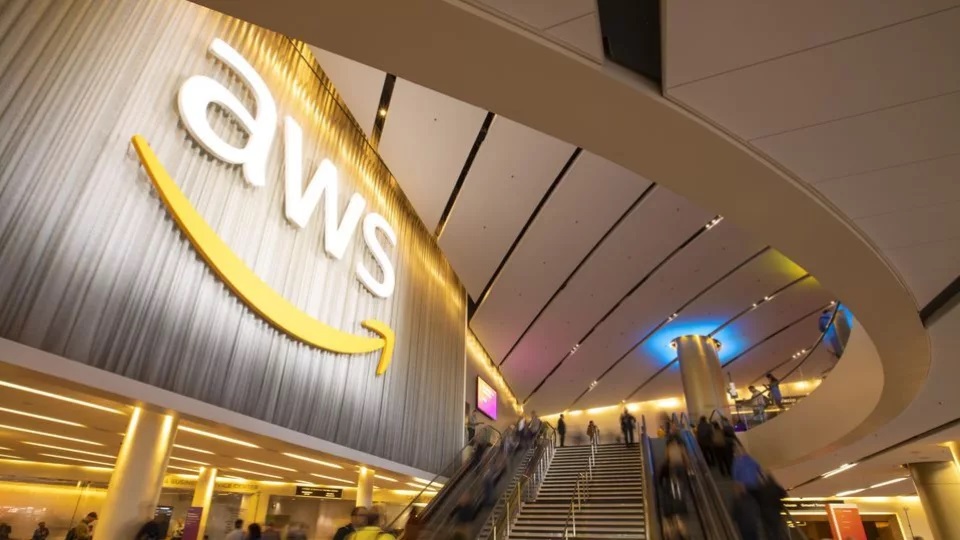
Under a new agreement, Swedish steel manufacturer SSAB will provide fossil-free steel to Amazon Web Services for use in construction of one of its three new data centers in Sweden. The program will see AWS receive steel from SSAB, as well as roof and wall structures for the buildings from SSAB’s subsidiary Ruukki. The main data center buildings are due for completion by mid-2025.
AWS has been working with various companies to use lower-carbon concrete, steel, and other materials for construction of its data centers, including these in Sweden, which have expanded in recent years because of increased demand for web-based services for AI and other technologies. Most of the steel used by AWS is made by recycling scrap in electric arc furnaces (EAF), which has only a quarter of the carbon emissions associated with steel made in blast furnaces (BF-BOF).
The new agreement follows an announcement earlier this year by SSAB of a decision to build a fossil-free mini-mill in Luleå, Sweden, capable of producing 2.5 million tonnes of carbon emission-free steel annually, which the company said would reduce Sweden’s CO2 emissions by 7%.
The new deal will see SSAB supply AWS with fossil-free steel, made using its HYBRIT technology, which largely eliminates the CO2 emissions from the steelmaking process altogether, producing just one-tenth of the carbon emissions of conventional BF-BOF steelmaking. Traditional steelmaking causes about 7% of global CO2 emissions, with both virgin and recycled steel production contributing to emissions.
Thomas Hörnfeldt, VP of Sustainable Business at SSAB, said:
“We are thrilled to welcome AWS as a new partner. By choosing steel made with the HYBRIT technology, AWS shows it’s possible to reduce the carbon footprint of data center construction regardless of whether the steel is made from scrap or virgin iron ore.”
The new steelmaking system used by SSAB was developed by the company together with iron ore company LKAB and energy company Vattenfall to replace the carbon-intensive BF-BOF production of virgin steel. Instead of coking coal, the HYBRIT technology uses hydrogen, produced with fossil-free electricity, to make sponge iron, which is then further processed into steel. This process emits water vapor instead of carbon dioxide.
AWS has worked with various companies in its supply chain to ensure that 70% of the structural steel used in several of its data centers in Sweden are derived from scrap-EAF sources, resulting in 10,000 fewer tons of embodied carbon emissions, the company said. However, the supply of such lower-carbon steel is limited; the International Energy Agency forecasts there will only be enough steel scrap generated in 2050 to meet 45% of global demand. To ensure that it can continue reducing its carbon footprint, AWS said that it has been working with companies to develop other methods of low-carbon steel production – and hence its deal with SSAB.
Kellen O’Connor, Managing Director Europe North at AWS, said:
“Reducing the embodied carbon associated with the construction of our data centers is a key priority for AWS as we work to achieve net-zero carbon across our operations by 2040. By partnering with innovative local companies like SSAB and Ruukki, we’re taking an important step to decarbonize the materials used in our data centers and set a new standard for sustainable infrastructure. We’re excited to be working with companies at the forefront of lower-carbon virgin steel production.”
Amazon has been taking other steps to reduce the carbon footprint of its data centers. In October, Amazon announced a series of new deals, and a $500 million investment, kicking off an expanded move to nuclear energy as a component of its strategy to address the increasing climate impact of its rapidly growing data center footprint. Amazon pledged in 2019 to match all of the electricity consumed across its global operations, including data centers, corporate buildings, stores and fulfillment centers, with 100% renewable energy by 2030.